V.ANDORbeyond
L'ALUMINUMSOR
NOTES
Aluminum is, in terms of abundance, the 3rd element after oxygen and silicon. Unfortunately, it is not found in nature in the metallic state but in the form di oxides, hydrates and silicates. of the metal is bauxite, a hydrate, in fact, di allumina, rock of a volcanic or sedimentary nature, of a color ranging from brown red to yellow, which has undergone in the course_cc781905-5cde-3194-bb3b- 136bad5cf58d_di ere a natural enrichment of aluminum.
LA PRODUCTION
The production of aluminum is divided into two phases:
1. Chemical phase: alumina extraction from bauxite;
2. Electrochemical phase: electrolysis of alumina in fused cryolite;
Four tons of bauxite produce two tons of allumina from which one ton of aluminum is obtained.

ALUMINUM ALLOYS
The pure aluminum is tight and ductile. This is a limitation because in most applications a level of mechanical resistance is required decisamente higher than what pure metal can offer. For this reason, aluminum is normally alloyed with other metals, in order to improve its characteristics.
The alloys di aluminium are divided into two categories: foundry alloys and plastic deformation alloys. Foundry alloys are particularly suitable for the realizzazione of castings and therefore to be cast in a mold. Plastic deformation alloys are suitable for undergoing a plastic transformation.
The effect of the alloying elements on the properties of aluminum depends not only on the nature and quantity of the added element but also on the modalities according to which the alloying si combines with aluminum and interacts with it on a microstructural level. The quantitative effects of alloying are also very evident: when the percentage by weight of the alloying elements increases, the hardening capacity obtainable in the alloy increases.
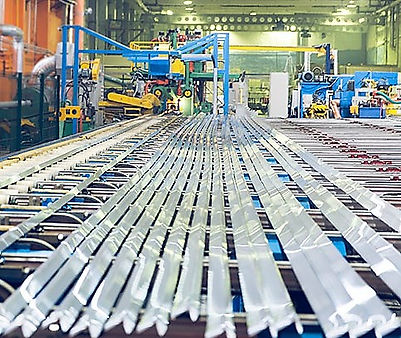
EXTRUSION
Extrusion is a process thermomechanical of hot plastic deformation, in which the metallic mass_cc781905-5cde-3194-bb3b-136b905c2cc5_constituent 136b58dcc5 5cde-3194-bb3b-136bad5cf58d_ is brought to the pasty state by heating to temperatures of the order of 500 ° C and subsequently pushed to the forced passage through a shaped opening, which gives the desired geometric shape.
The machine used for extrusion is the press. The heart of the process is the matrix made up in its simplest form by a disk di hot-formed steel in which a slot reproduces the shape of the profile to be obtained.
SURFACE TREATMENTS
As with many metals, surface treatments improve the functional and aesthetic properties of the alloys di allumin. The most known and widespread finishes for the alloys di alumin are anodizing powder and painting.
ANODISING
This process creates an oxide, with properties different from those of natural oxides and in particular, extremely hard to resist abrasion and corrosion. In the anodizing process, an electric current is passed into an electrolytic bath in which the pieces of aluminum are immersed.
PAINTING WITH POWDER PAINTS
Powder coatings come in the form of fine powders, 100% solid, totally solvent-free. The paint comes applied by means of an electrostatic gun on the grounded product. Subsequently the product is passed in the oven to allow the paint to harden, usually at temperatures between i 160 and 200 ° C. Once cooled, the product is ready for assembly or packaging. The thickness of the hardened film is conventionally in the order of 60-80 microns. Thanks to the film di high thickness and to the density of creticulation, their properties of resistance to corrosion obtain their resistance to powder coatings.
V.ANDORaluminum
Discover the profiles we use, the types of frames, colors, technical characteristics and any other information.